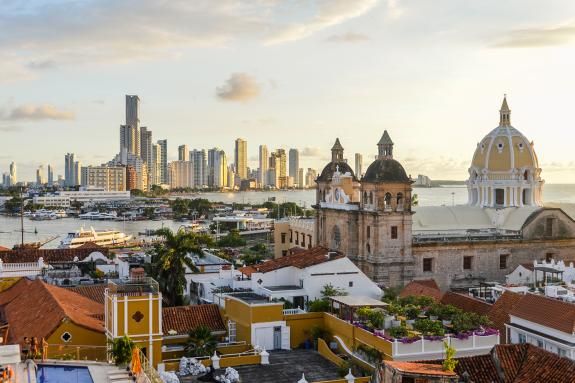
Our funds
Ashmore Colombia Fund I
Ashmore Colombia Fund I (“Fund I”) closed on approximately US$170 million in commitments in 2010. Ashmore Colombia has generated an additional US$67.5 million of co-investments, which combined with the original commitments and recycling, means that Fund I has committed approximately US$285 million to date.
Sector | Power / Generation |
Location | Yumbo, near Cali, Colombia |
Investment date | Dec-10 |
Overview
TermoemCali is a 235 MW co-generation gas-fired power plant located in the municipality of Yumbo, Colombia, which has been in commercial operation since 1999. The main components of the plant are: Combustion turbine generator; Heat recovery boiler (HRSG); Steam turbine generator; Condenser; Gas receiving and conditioning system; Demineralization water treatment plant; Cooling water uptake system form the Cauca River; Control system; Alternative fuel system (Fuel Oil): storage, management and metering systems; Transformers to join the generators with the Guachal substation; Administrative and control offices.
Backup power generating plant with two turbines: a combustion turbine (either natural gas or fuel oil) and a steam turbine that generate either during very dry seasons (during the El Niño phenomenon) or during peak demand, giving reliability to Colombia’s electric system.
Categorization
Category B project according to the IFC’s “Environmental and social review procedures manual”.
Environmental and social aspects
Environmental and social due diligence (“ESDD”), November 2010:
TermoemCali has had excellent environmental management and performance. Its relations with neighboring communities are positive. Both TERMOEMCALI’s ISO 14001 and ISO 9001 certifications are reflective of its good practice. Its social management record has been sound and reflects its good standing with stakeholders. Safety and security have been promoted throughout, and the plant has a strong occupational health and safety program and a good security and safety engagement with its workers and local community. TERMOEMCALI has established a complete Environmental and Social Management System (ESMS). This is reflected in the plant’s procedures, organizational culture, social responsibility programs and environmental audits. The plant was established after a fully-fledged environmental impact assessment. All the recommendations from the Environmental and Social Impact Assessment (ESIA or EIA in Spanish) and relevant national and local authorities have been adopted. All of the environmental permits are in place. Regular environmental audits have helped to detect and prevent any potential environmental problems. The plant has complied with the legal standards and requirements since the inception of the project. The operation with natural gas has been clean and safe. Stakeholders have not complained about TERMOEMCALI’s environmental performance, and it complies with the IFC’s Environmental Performance Standards.
Key E&S impacts and risks are those typically associated with the operation and maintenance phase of a power generation plant. These include hazardous waste generation, water use, wastewater generation and discharge, air quality and atmospheric emissions, GHG emissions, noise generation, risks associated with occupational health and safety, and contractor management. TERMOEMCALI is located 3 km from the nearest community (Vereda Piles) and does not generate negative social effects on ethnic minorities or on cultural heritage. The main positive impacts of E&S include power generation, hiring local labor, protection of natural resources, and social support.
Environmental and Social Key Aspects/ 2020:
- TERMOEMCALI continues to implement ESMS in accordance with legal regulations, IFC Performance Standards and World Bank EHS Guidelines. TERMOEMCALI is certified in ISO 9001 (Quality), ISO 14001 (Environmental), and ISO 45001 (Occupational Health and Safety).
- The environmental licenses and permits of TERMOEMCALI are under strict monitoring to ensure their compliance status. This is done through permanent inspection, documentary control, delivery of reports and internal environmental audit. TERMOEMCALI has no defaults or liabilities in environmental, social and occupational health and safety matters.#
- The solid waste generated is delivered to specialized managers who are in charge of its final disposal. Hazardous waste is taken to incineration in duly certified facilities. Suppliers collect some post-consumer waste such as plastic containers of chemicals, used batteries and fluorescent lamps. The use of plastic and polystyrene was eliminated, replacing them with biodegradable materials.
- TERMOEMCALI verifies the quality of the treated wastewater before discharge to the Cauca river through periodic monitoring. To avoid contamination of the Cauca river water, the following control systems have been installed: a.) Domestic wastewater treatment plant; b.) Oily water separator; c.) Rainwater ponds; d.) Neutralization tank.
- TERMOEMCALI has implemented activities to control and minimize the generation of GHG such as the use of natural gas, and fuel oil or biodiesel as backup fuel. NOx emissions are controlled by injecting demineralized water into the combustion zone of the turbine, reducing the temperature in front of the flame, and therefore the formation of NOx. During the operation stage, and every six months, air quality and isokinetic measurements are carried out complying with the regulations permissible limits.
- The noise reduction and control programs include the use of structural barriers against acoustic radiation, acoustic insulation of walls that surround turbines and boilers, silencers, vibration isolation devices, and adequate protective equipment for employees and visitors.
- TERMOEMCALI continues to voluntarily protect a Guadua Angustifolia Kunth plantation. These activities are framed in an annual work schedule where the plantation status is monitored conducting scheduled cleanups and fertilization.
- TERMOEMCALI facilities comply with what is established in the codes and technical regulations regarding earthquake-resistance, security and emergency systems (F&G, SDE, and FPS), etc. TERMOEMCALI has an updated contingency and emergency response plan, and they are working on developing a mutual aid plan with local authorities and neighboring companies.
- Within the framework of social responsibility, TERMOEMCALI has been working with the AHIMSA Foundation through a donation contract. Although there are no communities within the plant's area of influence (as established in the environmental management and control instrument), the Foundation has been working with the Vereda Piles, which is approximately 3 km away, providing information periodically and implementing some social programs.
- TERMOEMCALI and AHIMSA Foundation have an implemented and disclosed mechanism for the reception, management and timely response of requests, complaints and claims.
Sector | Logistics / Heavy lift transport |
Location | Tocancipa, Cundinamarca, Colombia |
Investment date | July 2011 |
Overview
Founded in 1978, MAMUT is Colombia’s market leader in logistics, heavy lift and specialized transport servicing the oil and gas, power, mining, industrial and construction sectors. The site where MAMUT’s headquarters are located is a highly consolidated industrial area, hosting a variety of manufacturing and service installations. Headquarters are located in the municipality of Tocancipá and include a patio area for equipment storage and preventive maintenance, and a building to house the administrative and managing areas. Satellite locations are installed in the main regional areas served by the company. In 2017, MAMUT de Colombia SAS changed its Company Name for MAXO SAS.
Categorization
Category B project according to IFC’s “Environmental and social review procedures manual”.
Environmental and social aspects
Environmental and social due diligence (“ESDD”), June 2011:
MAMUT (MAXO) has established a solid Environmental and Social Management System (ESMS), embedded within a quality-oriented management approach, based on safety. This is reflected in the company’s procedures and organizational culture. MAMUT’s operations do not present relevant environmental risks, as its transport services take place on existing transport infrastructure with previously assessed conditions. The company’s management includes safety with loading, transporting and unloading extra size and heavy cargo, presenting potential risks for workers, drivers, local communities, equipment, and property. Therefore, emphasis is placed on a strong safety culture and operating procedures to effectively mitigate these risks. Not only is it necessary to prevent accidents, but in the event of any accident, it is important to effectively minimize any potential impact. In addition, it is necessary to learn from the experience to prevent future similar events. MAMUT has achieved strong occupational health and industrial safety standards, and has received an OHSAS 18001 certification. Improvements can be made in the claim and response system, to attend not only clients, but stakeholders in general. Social responsibility to the neighboring communities can be strengthened to attend local stakeholders’ needs. Nonetheless, the company’s overall ESMS is sound and properly focused on safety. MAMUT complies with the IFC’s Environmental Performance Standards.
Key E&S impacts and risks are those typically associated with roads and bases operation (heavy lift and specialized transport). These include hazardous waste generation, wastewater generation, air quality and GHG emissions, noise generation, pesticide use, health and safety risks (occupational accidents, traffic accidents, and emergencies), security risks, contractor management, and social impacts for the communities near the bases and the roads used. MAXO´s operation does not generate social negative effects such as affectation of vulnerable groups or ethnic minorities, or affectation of significant cultural heritage sites. The main positive impacts of E&S include hiring of local labor and social support.
Environmental and Social Key Aspects/ 2020:
- MAXO has developed an Environmental, Social, and Occupational Health and Safety Management System, which it continues to implement in compliance with legal regulations, IFC Performance Standards and World Bank EHS Guidelines. MAXO is certified in ISO 9001 (Quality), ISO 14001 (Environmental and Social), and OHSAS 18001 (Occupational Health and Safety).
- MAXO does not require licenses, permits or environmental authorizations at its main base (Tocancipá). Water supply, wastewater management, and solid waste management are done through utility companies. In the different operating bases, MAXO clients are responsible for obtaining and complying with the required environmental permits. All contracts signed by MAXO and its clients establish requirements to comply with environmental and health and safety regulations.
- MAXO has a hazardous and non-hazardous waste management plan. Final disposal of waste is carried out with environmentally certified and authorized companies. MAXO's operating process does not generate significant wastewater discharges. Domestic wastewater at the bases is delivered to sewage systems.
- Emissions of atmospheric pollutants generated by MAXO's operations are within the permissible regulatory limits, since they are related to the transport fleet, which is relatively new. MAXO performs annual measurements of the carbon footprint (its results are less than 5000 tons of CO2eq per year). Control measures are carried out to mitigate and control GHG emissions in terms of waste management, efficient use and saving of resources (water and energy), and maintenance management of equipment and vehicles (technical-mechanical and gas inspections).
- MAXO has a set of procedures for safely lifting, loading/unloading, and transporting extra-heavy loads. In addition, MAXO has an annual training, skills development, and awareness program, which includes topics such as: Safety (risk and hazard prevention), work at heights, transport logistics for extra-heavy cargo, load lifting, crane handling, safe work, road safety, psychological and social risks, equipment and tools, environmental management, hygiene and preventive health (including Covid-19 prevention and management), response to emergencies, continuous improvement, among others.
- MAXO has an updated emergency plan for the bases, which includes guidelines for the prevention, preparation and response to emergencies, the formation and training of an integrated emergency squad, simulations, etc. In addition, MAXO has a road safety plan, which defines the vehicular revision, inspection of overnight points, road studies prior to mobilization, preventive maintenance plan, and road patrols.
- Most of the MAXO bases (Tocancipá, Cerrejón and Puerto Boyacá) are located outside urban centers, so there is no direct impact on the communities. In other locations (Arauca and Barranquilla), the base walls allow the isolation and protection of the daily activities of the surrounding communities. In the transport exercise, measures are taken such as planning and studying the route before mobilization, risk analysis for the location of power lines, rotation angles, night spots, etc. In the bases, there are private security companies. On the roads, there is an external security adviser with links to the security forces. The security administration has been complying with the IFC PS4 guidelines.
- The clients to whom MAXO provides its services are directly responsible for social management with neighboring communities. However, through the OKAMANDO Foundation, MAXO provides regular information to the communities and carries out different social support activities (social work, donation of recyclable waste, etc.).
Sector | Transportation / Buses |
Location | Cartagena, Colombia |
Investment date | November 2014 |
Overview
Cartagena is the second largest city on the Colombian Atlantic coast with approximately 990,000 inhabitants. The municipality has implemented a Bus Rapid Transit (“BRT”) system, “TRANSCARIBE”, integrating the city’s transport system. TRANSAMBIENTAL is one of the system's operating concessionaires. BRT is a more efficient transport system for the city of Cartagena with at least the same number of passengers as previously able to travel on fewer vehicles, with better service and comfort levels. Importantly a large number of buses from the old fleet is being retired from service and scrapped. As a result, less fuel is used leading to lower levels of emissions of Green House Gases (GHG) and air pollutants.
Categorization
Category B project according to the IFC’s “Environmental and social review procedures manual”.
Environmental and social aspects
Environmental and social due diligence (“ESDD”), September 2014:
From an environmental and social point of view, considering IFC’s Sustainability Framework, the project Transcaribe Mass Transportation System represents low risk. This assessment also considers the Concessionaire’s commitment to identify, prevent, mitigate and solve all possible environmental and social risks and to fully comply with Colombian regulations and the IFC performance standards. This will allow proper prevention and control of pollution events. The formulation and implementation of the Environmental and Social Management System (ESMS) has been required in order to fully comply with the IFC PS. This secures a high level of environmental and social performance during the operation of the system. The strengthening of the policies and procedures related to working conditions and the creation of communication channels that facilitate the interactions of the workers and employees with TRANSCARIBE have been crucial to fully comply with the IFC PS.
Key E&S impacts and risks are those typically associated with the operation and maintenance of the bus fleets. These include hazardous waste generation, water use, wastewater generation, rainwater pollution, air quality and vehicle emissions, GHG emissions, noise generation, pesticide use, health and safety risks (occupational accidents, traffic accidents, and emergencies), security risks, contractor management, and social impacts for passengers and nearby communities. TRANSAMBIENTAL’s operation does not generate social negative effects such as affectation of vulnerable groups or ethnic minorities, involuntary displacement and resettlement, or affectation of significant cultural heritage sites. The main positive impacts of E&S include the provision of a massive public transport service, the reduction of users' travel times, the improvement of traffic, the reduction in gas emissions, the hiring of local labor and social support.
Environmental and Social Key Aspects/ 2020:
- TRANSAMBIENTAL has developed an Environmental, Social and Occupational Health and Safety Management System, which it continues to implement in accordance with national legislation, IFC Performance Standards and World Bank EHS Guidelines. TRANSAMBIENTAL is ISO 9001 (Quality) certified, and plans to obtain the 14001 (Environmental) and 45001 (SST) certifications.
- The environmental permits of TRANSAMBIENTAL are under strict monitoring to ensure their compliance status. TRANSMBIENTAL has no defaults or liabilities in environmental, social and occupational health and safety matters.
- TRANSAMBIENTAL has a management plan for hazardous and non-hazardous solid waste, through which it establishes the procedures for separation at the source, collection, temporary storage, transportation and final disposal with authorized managers.
- TRANSAMBIENTAL also has a management plan for hazardous materials, through which labeling, signaling, temporary storage and safe use measures are guaranteed. This program restricts the use of hazardous materials subject to international prohibitions or gradual elimination.
- Domestic wastewater generated at TRANSAMBIENTAL's facilities is discharged into the sewer system. The wastewater generated in the maintenance areas is collected in pits and grease traps, and delivered to authorized managers for final disposal. The wastewater generated by the bus fleet's washing activities is sent to a treatment plant and recirculated 100%. Rainwater is collected through a system of gutters and grease traps, before being discharged into the environment. TRANSAMBIENTAL has implemented a water saving and efficient use program, focused on monitoring, reduction and reuse strategies.
- The operation of the bus fleet (which runs on natural gas) has improved air quality and the well-being of the community by reducing atmospheric emissions. TRANSAMBIENTAL annually conducts air quality monitoring, obtaining to date results that are within regulatory limits. Although GHG emissions have also been reduced, due to the progressive and technological replacement of the bus fleet, Ashmore has recommended TRANSAMBIENTAL to carry out an annual diagnosis of the GHGs generated and define mitigation measures.
- TRANSAMBIENTAL has a contingency and emergency response plan based on an analysis of risks, which provides the necessary tools to ensure preparedness and response to different emergencies. TRANSAMBIENTAL also has a road safety plan, which defines actions to persuade, train, inform and induce the proper use of infrastructure and to guide users (drivers, passengers, pedestrians and cyclists) in the perception, recognition and management of risks. The objective of this plan is to reduce accidents, contribute to the reduction of human and material losses, and strengthen a civic culture in relation to the safe and comfortable use of the transport system.
- The company manages the prevention of accidents and occupational diseases, and the protection and promotion of workers' health. To do this, TRANSAMBIENTAL carries out risk analysis and procedures for critical tasks, training and education for employees, EHS inspections, internal audits, Covid-19 management, etc.
- TRANSAMBIENTAL develops permanent and continuous work with the communities and the users of the transport system through different social management programs: i) Information and participation. ii) Citizen culture (“100% Users” and “My trans-Caribbean culture"). iii) Hiring of local labor. iv) Support for the restoration of the socioeconomic conditions of those affected by the change in the transportation system. v) Creation of the "Moving Hearts, Building Dreams" volunteerism (employee support for vulnerable families).
- To ensure compliance and proper functioning of the TRANSAMBIENTAL’s grievance mechanism, a monthly committee was established with TRANSCARIBE, where criteria are unified, complaints are evaluated, and recommendations are made.
Sector | Transportation / Roads |
Location | Colombia |
Investment date | July 2015 |
Overview
Part of the Colombian government’s flagship US$20 billion Fourth Generation “4G” road infrastructure program. Ruta del Cacao, also known as the “Bucaramanga – Barrancabermeja – Yondó” project, involves the construction of an interconnection between the city of Bucaramanga and the western part of the Department of Santander, and the connection of the municipality of Yondó in the Department of Antioquia with the Ruta Del Sol II concession. The Project is a concession to construct, rehabilitate, and improve the roads involved in the road interconnection. The road is divided into Nine Functional Units (FU) and has a total length of 191 km. Ruta del Cacao will reduce the travel time between Bucaramanga and Barrancabermeja by over 35% and generate savings of approximately US$1 billion in travel time, vehicle operation costs, and environmental impacts.
Categorization
Category A project according to IFC’s “Environmental and social review procedures manual”.
Environmental and social aspects
Environmental and social due diligence (ESDD), 2015:
In order to obtain the licenses, the Consortium has been preparing a comprehensive Environment and Social Impact Assessment (ESIA) addressing the cumulative impacts of all the road segments. The Project must comply with different requirements for the various road segments, bringing complexity to the environmental licensing process. For the areas not covered by licensing requirements, Ashmore Colombia with the support of E&S specialists, will design potential resettlement implementation plans, as well as establish additional budget allocations, in line with IFC Performance Standards requirements. The following items are being part of the ESIA (Environmental and social impact assessment): Erosion and sediment control plan, environmentally sensitive areas management plan, biodiversity compensation plan (tropical rain forest), ecosystem services program, ecological restoration plan, forest management plan, integrated vegetation management plan, disaster risk evaluation and disaster risk management plan, hazardous waste management plan, solid waste management plan, storm water management plan, construction material management plan, infrastructure and equipment design safety plan, vehicle and machinery maintenance and repair plan, decommissioning and final restoration plan, resettlement action plan, livelihood restauration plan, land acquisition plan, chance find procedures, grievance mechanism, and long-term indirect impacts control plan.
Key E&S impacts and risks are associated with the construction and operation phases of a road infrastructure project. These include alteration of land and landscape, erosion and sedimentation, removal of vegetation cover, biodiversity alteration, use of hazardous materials, hazardous waste generation, water use, wastewater generation, rainwater pollution, air quality and pollutant emissions, GHG emissions, noise generation, health and safety risks (occupational accidents, traffic accidents, and emergencies), security risks, contractor management, land acquisition, cultural heritage and social impacts for nearby communities (including social negative effects, such as the affectation of vulnerable groups, involuntary displacement and resettlement). The main positive impacts of E&S include the provision of a high-performance road, the reduction of user travel times, the improvement of traffic, the hiring of local labor and social support.The Project must comply with different requirements for the various road segments, bringing complexity to the environmental licensing process.
Environmental and Social Key Aspects/ 2020:
- "Ruta del Cacao Concession (CRdC)” has developed and implemented an Environmental, Social and Occupational Health and Safety Management System based on national legislation, IFC Performance Standards and World Bank EHS Guidelines.
- CRdC already has the environmental license and the necessary environmental permits for the construction and operation of all functional units (FU). FUs 2, 3 and 4 have already entered into operation, works are being completed on FUs 5, 6 and 7, and works are beginning on FUs 8 and 9. CRdC has been advancing the land acquisition process with the support of the CONSULTORIA COLOMBIANA contractor, and with the construction process through the EPC FERROCOL contractor. Within the framework of this management, the environmental and social management plan approved in the environmental license and in the other permits granted (including the environmental programs established in the “PAGAs” (Adaptation Plan to the Environmental Guide, required by INVIAS) for operation, maintenance and rehabilitation) has been implemented. Ashmore has recommended to CRdC/FERROCOL integrate the environmental and social management with construction activities in order to guarantee compliance and avoid deviations especially at critical points such as crossings with water sources, sites of final disposal of excavation materials, tunnels and access. Likewise, strengthen environmental and social inspection and monitoring activities on work fronts in order to ensure compliance with the environmental license.
-
Considering that in the area of influence of the project are the “Regional Districts of Integrated Management San Silvestre and Serranía Los Yariguíes", and strategic areas for conservation such as the tropical dry forest, CRdC/FERROCOL have been implementing actions to the protection and conservation of biodiversity within the framework of biotic compensation plans: i) Forced investment of 1%; ii) Compensation for loss of biodiversity; iii) Rescue and transfer of epiphytes; iv) Landscape compensation.
-
In terms of occupational health and safety, CRdC/FERROCOL have been developing the following activities in order to guarantee safe and healthy work environments: Induction and training; Handling of hazardous materials; Delivery of personal protection items; Risk analysis and work permits for critical tasks; Emergency preparedness and response; Preventive medicine and self-care (including Covid-19 prevention and management); Inspections of machinery, equipment and construction fronts; Report and follow-up on unsafe conditions, work accidents and occupational diseases; Road safety and traffic management; Teamwork and interpersonal relationships; Order and cleanliness.
-
CRdC/FERROCOL have been carrying out the following activities in social matters: i) Information and participation; ii) Support for institutional management; iii) Education and awareness; iv) Road safety; v) Hiring of local labor; vi) Accompaniment to socio-property management (includes plans for land acquisition, resettlement and socio-economic compensation); vii) Archaeological heritage management (includes prospecting, monitoring and rescue processes as required in the preventive archeology program and archaeological management plan); viii) Grievance mechanism (CRdC has 6 offices installed to receive and attend to community requests, complaints and claims); ix) Social responsibility (construction and operation of 2 community aqueducts in Portugal and Villa Maria). Since 2019, CRdC has been working on the implementation of a social action plan, in which progress has been made with the following actions: i) Updating of the matrix of social actors and communication plan; ii) Definition of the social strategy for the management of Veedurías Comunitarias and communities of FUs 5, 6, 7, 8 and 9. With regard to the social responsibility plan committed to the ANI (National Infrastructure Agency), progress is being made with the design of the municipal aqueduct system of Villa Maria, San Silvestre and El Pozo, and with the activities of road safety and education to the community.
Sector | Education |
Location | Colombia |
Investment date | July 2018 |
Overview
REDCOL S.A.S. is a Colombian company that works in the creation, direction, administration, operation and consultancy of educational projects with multilingual and complementary content through personal and collective support programs. It works with institutions of preschool education, basic primary, secondary, vocational media, technology and higher education, formal and non-formal, and provides all complementary services to the educational object, such as Nursing, Nutrition, Speech Therapy, Occupational Therapy, Psychology, Library, Computer science and technology, and restaurant service for children from 4 months of age, ensuring academic quality and sustainability in all their activities.
Categorization
Given the nature of REDCOL activities and its schools, those are aligned with the Category B for the International Financial Corporation (IFC) and the Environmental and Social Management System (ESMS) of AAFII: "Business activities with possible risks and / or adverse environmental or social impacts of a limited nature that are scarce in number, generally located in specific sites, mostly reversible and easily addressed through mitigation measures". In this way, it is considered that the risks identified for the REDCOL´s schools are mitigable, reversible and limited in number and extent; likewise, it is not considered that these impacts may have a greater scope to the areas of the property where the Schools are located.
Environmental and social aspects
Environmental and social due diligence (“ESDD”), 2017-2020:
From the environmental and social point of view, considering IFC’s Sustainability Framework, the project represents medium risk. The project´s commitment is to prevent, mitigate and solve all possible environmental and social aspects, and to comply with national regulations and with the IFC Performance Standards. REDCOL has limited potential to generate adverse environmental, social risks and/or impacts. Those impacts, if any, would be few in number, site-specific, largely reversible, and readily addressed through mitigation measures in accordance with Category B projects. The REDCOL´s schools has not had any significant environmental or social issues.
The formulation and implementation of the Environmental and Social Management System (ESMS) has been required in order to comply with IFC PS. This secures a high level of environmental and social performance during the operation of the system. As priority items, the project should run:
- An Environmental, Social and Occupational Health and Safety Management System, including the assignment of responsible for ESG management of REDCOL.
- Prepare and disclose the Environmental Social and Occupational Health and Safety Policy.
-
Establish unified management guidelines for schools to comply with environmental legislation, Environmental and social sustainability Performance Standards of the IFC (International Finance Corporation), Environment and Health and Safety Guide of the World Bank, and implementation of the Environmental and Social Action Plan (ESAP). As part of these guidelines should be established: i) work plan, procedures / documents of base management, ii) control to contractors and suppliers, iii) establish a base of indicators, iv) guidelines for the presentation of unified reports, v) notification of serious incidents, vi) periodic follow-up visits, vii) internal audit programs, and ix) Communications.
-
A hazardous waste and wastewater management programs.
In addition, some development opportunities for REDCOL schools include review and update of licenses and certificates, wastewater management, solid waste management, electrical connections, gas installations, food preparation, water use, among other aspects.
The REDCOL Schools are: 1. Colegio Británico de Cartagena S.A.S; 2. Gimnasio Vermont Medellín S.A. (Medellín, Antioquia); 3. Colegio Nuevo Cambridge S.A.S (Bucaramanga, Santander); 4. Kínder DC and Colegio La Arboleda S.A.S (Cali, Valle); 5. Colegio Nuevo Cambridge Valle S.A.S (Cali, Valle); 6. Colegio Gimnasio del Norte Valledupar S.A.S (Valledupar, Cesar); 7. Colegio Amigos de Bureche S.A.S (Santa Marta, Magdalena); 8. Colegio New Port S.A.S (Bucaramanga, Santander); 9. Colegio Santa Francisca Romana S.A.S (Bogotá).
Key E&S impacts and risks are those typically associated with the schools operation and maintenance. These include hazardous waste generation, water use, wastewater generation, noise generation, pesticide use, health and safety risks (exposure to physical, biological, ergonomic and psychosocial risks, occupational accidents, traffic accidents and emergencies), supplier management, security risks, and social impacts for nearby communities. REDCOL’s operation does not generate social negative effects such as affectation of vulnerable groups or ethnic minorities, or affectation of significant cultural heritage sites. The main positive impacts of E&S include the provision of the educational service, hiring of local labor and social support.
Key Environmental and Social aspects (2020):
-
REDCOL schools have an environmental, social and occupational health and safety management system, which is in the process of implementation and continuous improvement to comply with national regulations, IFC Performance Standards and World Bank EHS Guidelines. Ashmore has recommended to REDCOL to ensure that the scope of the management system includes all schools, in order to implement the same policies, guidelines, standards, procedures, plans and programs.
-
Some schools are in the process of modernizing their facilities, for which compliance with seismic-resistant regulations, electrical regulations, firefighting systems, emergency response elements, furniture and public services has been guaranteed.
-
The permits, licenses and authorizations of the REDCOL schools are in force and in compliance: i) Delivery of quality monitoring reports of wastewater; ii) Registration and delivery of reports of hazardous waste; iii) Certificates of sanitary suitability; v) Certificates of compatibility of land use and construction licenses; vi) Certificates of the firefighting system. REDCOL schools have no defaults or liabilities in environmental, social and occupational health and safety matters.
-
REDCOL manages its E&S impacts and risks through the following programs and actions: i) Saving and efficient use of water and energy: change of sanitary equipment, replacement of water dispensers, use of natural light and reduction of electricity consumption, use of LED lights, and installation of motion sensors. ii) Efficient use of paper: controlled use of impressions. iii) Control of wastewater discharge: treatment before discharge to the sewer, periodic monitoring (through certified laboratories) and verification of regulatory compliance. iv) Solid waste: management of hazardous and non-hazardous waste through source separation, collection, temporary storage, transportation and final disposal with authorized managers. Installation and signaling of ecological points and recycling. v) Conservation and protection of biodiversity: Protocol of species (fauna and flora); School garden project (planting and harvesting of vegetables); tree sowing; Composting project (use of organic waste); Use of biodegradable materials. vi) Pest control: control of arthropods, rodents and insects. vii) Annual measurement of the carbon footprint (quantification of GHG emissions).
-
In terms of occupational health and safety, REDCOL and its schools, within the framework of the management system, carry out various activities to guarantee the prevention of accidents and occupational diseases such as training and education for employees, promotion and prevention in health (including Covid-19 prevention and management), management of dangerous substances, delivery of personal protection items, management of Covid-19, etc. The Official Fire Department periodically certifies the fire extinguishing system of REDCOL schools, and its elements and emergency response equipment. The competent authorities have also certified the emergency preparedness and response plan, where the risks are analyzed and the actions for prevention, preparation and response to emergencies are defined. Ashmore has recommended a detailed review of the fire safety system at each site following international standards. REDCOL schools also have a strategic road safety plan to control risks derived from the transportation service.
-
In terms of social management, REDCOL and its schools have been implementing the following programs: i) "Amparo" Program: Scholarship students throughout their entire school education. ii) Creation of social impact tables in each city with the participation of external actors in order to agree on social projects. iii) Continuity of social projects in each school: Children of the San José Home, Santa Ana Asylum, Los Salados public school, Social projection in the Oasis - El Hormiguero community, Childhood-Adolescence connection, Sagrado Corazón de Jesús geriatric, Los Campanos cultural and entrepreneurship center, Santa Francisca Romana Dispensary, etc. iv) Social support: Donation of used school furniture, Delivery of full scholarships for children from vulnerable families, Social service, etc.
-
REDCOL schools have an implemented and disclosed mechanism for the reception, management and timely response of petitions, complaints and claims (grievance mechanism).
-
Regarding security, REDCOL has carried out a periodic update of the analysis of security risks in each school, continuous monitoring by cameras, monitoring and training of private security personnel (human rights, rules of conduct and behavior, response to emergencies, etc.), and prohibition of use of arms.
Ashmore Andean Fund II
Ashmore Andean Fund II is a closed and long-term private equity fund that makes investments in assets related with infrastructure projects in Colombia, Peru, Panama, Costa Rica, El Salvador and Guatemala. The Fund has a parallel fund based in Canada, in order to facilitate investment processes for those investors domiciled in jurisdictions other than Colombia.
Sector | Power - Transmission Line |
Location | Riohacha, Maicao and Cuestecitas, La Guajira, region located in Colombia's northern coast. |
Investment date | November 2016 |
Overview
The company develops the construction of two transmission lines 110 kV, one between Riohacha and Maicao (La Guajira) and another between Riohacha and Cuestecitas (La Guajira). Aditionally, some investments in substations at Riohacha, Maicao and Cuestecitas are considered. The project comprises:
-
A line of 110 kV of approximately 62 kilometers length, between Riohacha and Cuestecitas substations.
-
A line of 110 kV of approximately 74.8 kilometers between Riohacha and Maicao substations.
-
A bay line of 110 kV in double bar configuration in Cuestecitas (110 kV Substation), for the new Riohacha Line - Cuestecitas.
-
Two bays line of 110 kV line in simple bar configuration at Riohacha Substation. One of the bays is for the new Riohacha Line - Cuestecitas and the other is for the new Riohacha Line - Maicao.
-
A new line bay of 110 kV, single bar configuration in Maicao Substation for connection of the new Riohacha Line - Maicao.
Categorization
Category A project according to the IFC’s “Environmental and social review procedures manual”.
Environmental and social aspects
Environmental and social due diligence (“ESDD”), September 2016:
The development opportunities of the project include:
-
Need of energy reliable supply in the area where the project is located.
-
The area where the project is located corresponds to sites previously intervened by other similar projects, so communities understand the risks and impacts.
-
Employment generation for local communities.
-
Contribution to communities’ current conditions through development programs.
From an environmental and social point of view, considering IFC’s Sustainability Framework, the project represents medium risk. This assessment also considers the project´s commitment to prevent, mitigate and solve all possible environmental and social aspects, and to fully comply with Colombian regulations and with the IFC standards.
The formulation and implementation of the environmental and social management system (ESMS) has been required in order to fully comply with IFC standards. This secures a high level of environmental and social performance during the operation of the system. As priority items, the project should run:
Environment and Social Governance structure, E&S and Security capacity:
In the construction and implementation the company shall:
-
Guarantee that all aspects of the project such as organization, design and implementation are in full alignment with the IFC Performance Standards;
-
Assure that impacted communities and indigenous peoples consultations are performed as per IFC’s Free, Prior and Informed Consent (FPIC) framework when applicable, which may exceed the requirements of the Colombian Prior Consultation process. Adequate budget allocation for full implementation of FPIC shall be included in the overall project cost;
-
The E&S and Security capacity through the creation of E&S and Security department with full time dedicated staff.
ESMS in alignment with IFC Performance Standards:
The ESMS will be designed and implemented in alignment with the IFC Performance Standards. The ESMS shall:
-
Establish clear roles and responsibilities and identify specific individual for all key positions;
-
Maintain commitment to assess, identify and manage E&S risks;
-
Establish monitoring and reporting requirements;
-
Design a Grievance Mechanism that will assure that affected communities will have a direct channel of communication with senior management and that appropriate actions are taken to address grievances
Perform an extensive Risk Assessment to further map all potential risks and impacts:
The company will conduct a comprehensive risk assessment of the overall project including project alternatives analysis, permitting, stakeholder engagement, prior consultation/FPIC, design, construction and operation. The risk assessment shall include security risks to project workers, communities and facilities. The risk assessment shall identify appropriate mitigation actions for all identified risks. The risk assessment shall be updated on a continuing bases throughput the life of the project.
Design detailed licensing/FPIC plan:
In order to obtain all necessary environmental licenses and complete required Prior Consultation/FPIC to meet the project schedule, the Company shall prepare a comprehensive Environment and Social licensing plan that addresses:
-
Transmission line route alternatives analysis
-
Environmental and Social Impact Assessment addressing all phases of the project and potential cumulative impacts
-
All other required environmental and social permits and approvals
-
Stakeholder engagement
-
Prior Consultation/FPIC
IFC and Ashmore Monitoring:
The company shall accommodate for supervision visits of an E&S officer of Ashmore and an IFC appointed specialist for the Guajira project. The monitoring site visits will take place on a quarterly basis during the first year and on a semester basis in the second and third year.
Key E&S impacts and risks are associated with the construction and operation phases of an electrical transmission line project. These include alteration of land and landscape, removal of vegetation cover, biodiversity alteration, use of hazardous materials, hazardous waste generation, water use, wastewater generation, air quality and pollutant emissions, GHG emissions, noise generation, health and safety risks (occupational accidents and emergencies), security risks, contractor management, land acquisition, cultural heritage and social impacts for nearby communities (including social negative effects, such as the affectation of indigenous people and vulnerable groups). The main positive impacts of E&S include the provision of reliable electricity to vulnerable communities, the hiring of local labor and social support.
Environmental and social key aspects/ 2020:
-
ELECNORTE and its main contractor (CDEM, MORELCO, DV INGENIERÍA and GEOCOL) have developed and implemented an Environmental, Social and Occupational Health and Safety Management System based on national legislation, IFC Performance Standards and World Bank EHS Guidelines.
-
ELECNORTE already has the environmental license and the necessary environmental permits for the construction and operation of the project. ELECNORTE has no defaults or liabilities in environmental, social and occupational health and safety matters.
-
ELECNORTE ended construction activities in October 2020 and began the operation and maintenance phase. The management carried out by the environmental, social and occupational health and safety team, through the identification and evaluation of risks and impacts, and the implementation of measures and controls, has allowed adequate integration during the construction stage. To continue in this same line during the O&M phase, ELECNORTE has proceeded to update its environmental, social and occupational health and safety management system.
-
In environmental matters, ELECNORTE and its contractors have carried out the following activities: i) Training and awareness campaigns. ii) Implementation of the environmental management plan (including waste and wastewater management, hazardous materials management, monitoring and control of polluting emissions, saving and efficient use of water and energy, rescue and relocation of fauna and flora, among other actions). iii) Annual measurements of the carbon footprint for construction phase (with results below 1,000 tons of CO2eq per year). iv) Decrease in the number of trees removed (although the environmental authority granted ELECNORTE a forest use permit for the removal of 2,360 trees, only 843 individuals have been removed). v) Rescue and proper management of Epiphytes (with a survival rate greater than 95%).
-
ELECNORTE has been implementing actions for the protection and conservation of biodiversity such as: i) Design with towers and spans higher than others located outside the protected area; ii) Installation of flight diverters; iii) Compensation for forest intervention; iv) Compensation for removal or relocation of national/regional protected species. For these compensations, ELECNORTE has focused its efforts on three priority conservation areas: a) Laguna Salá complex, for the design of environmental recovery works; b) Rancho Grande area, for conservation, natural enrichment and passive restoration; c) Santa Bárbara area, for the relocation of the Epiphytes.
-
Regarding occupational health and safety, ELECNORTE and its contractors have carried out the following activities: i) Induction, training and education of employees. ii) Handling of hazardous materials. iii) Delivery of personal protection items. iv) Risks analysis and work permits for critical tasks. v) Equipment maintenance. vi) Emergency preparedness and response. vii) Permanent monitoring of the health conditions of employees (including Covid-19 management). viii) EHS inspections of contractors. ix) Report and monitoring of unsafe conditions, work accidents and occupational diseases. x) Road safety. All these activities will continue to be implemented during the O&M stage. Ashmore has recommended updating the contingency and emergency response plan considering the risks of the O&M stage (electrocution, electromagnetic interference, noise, safety in air navigation, forest fire, etc.), and socialize it with communities and local authorities.
-
In social matters, ELECNORTE and its contractors have been carrying out the following activities: i) Information and community participation. ii) Training, education and community awareness. iii) Accompaniment to socio-property management. iv) Hiring of local labor. v) Social compensation. vi) Management of archaeological heritage. ELECNORTE has signed social compensation agreements, within the framework of IFC’s Free, Prior and Informed Consent (FPIC) with 4 Indigenous Communities of the Sierra Nevada de Santa Marta, 6 Councils of Black Communities and 145 Wayuu Communities. The prior consultation commitments are expected to close in 2021, with the corresponding closing act issued by the Ministry of the Interior.
-
ELECNORTE has a security management plan in line with national legislation and recommended international practices in matters of recruitment, standards of conduct, training (uses and customs of the Wayuu community, human rights, rational use of force, voluntary principles), equipment and supervision of security personnel.
Sector | Power - Transmission Line |
Location | The installations and facilities making up the Power Plant will be located in the “El Morro”, municipality of Yopal, Casanare, Colombia. |
Investment date | November 2016 |
Overview
The power plant will have an electricity transmission line (115 kV power capacity, 20m right-of-way and a length of approximately 16,1 km) and a carbon steel flow line to transport natural gas (6” diameter, 10 m right-of-way and a length of 1,8 km) that corresponds to the principal fuel at the plant. The plant is made up of three (3) compact modular power plants with the capacity to generate 19.6 MW, so the power plant will generate a total of 58,8 MW.
Categorization
Category B project according to the IFC’s “Environmental and social review procedures manual”.
The project is classified as category B, as the area where it is located is intervened by other linear and punctual projects of the energy sector (primarily hydrocarbons), so that the environment is modified and communities are not considered highly vulnerable in their relationship with the companies, and therefore impacts and risks are limited, specific, reversible and easily addressed through prevention, mitigation and control measures.
Environmental and social aspects
Environmental and social due diligence (“ESDD”), July 2016:
The development opportunities of the project include:
-
There is a clear need for energy in the area where the project is located.
-
The area where the project is located corresponds to sites previously intervened by other projects, so communities have experience and knowledge in implementing industrial activities and ecosystems with a high environmental conservation and/or sensitivity are not involved.
-
Employment generation for local communities.
-
The proposal of the plan of social responsibility to support the improvement of the network of distribution and production of energy for the community.
-
The project has an environmental license for the implementation of its activities and to date, the environmental authority has no objection to MECHERO ENERGY management of the project.
From an environmental and social point of view, considering IFC’s Sustainability Framework, the project represents low risk. This assessment also considers the project commitment to prevent, mitigate and solve all possible environmental and social aspects, and to fully comply with Colombian regulations and with the IFC standards.
The formulation and implementation of the environmental and social management system (ESMS) has been required in order to fully comply with IFC standards. This secures a high level of environmental and social performance during the operation of the system. As priority items, the project should run:
-
TERMO MECHERO is a company committed to its environmental, social and H&S performance; moreover it has a Coordination team able to assimilate the challenges and improvements that can be required; however, the Team should be trained (in IFC Performance standards, risk identification, contractors supervision and management system) and assess the need to hire support employees as part of the coordination Team directly or through the involved contractors. Likewise, a risks identification procedure should be elaborated and implemented, as well as an action plan to mitigate the risks identified.
-
Complement the current existent and applicable information of the project, strengthen and implementing an integrated, centralized and comprehensive environmental and Social Management System (ESMS). The ESMS should incorporate at least the following elements: i) policy; ii) ecosystem services assessment; iii) identification of risks and impacts (including the analysis of cumulative and residual impacts); iv) management programs; v) organizational capacity and competency; vi) emergency preparedness and response; vii) stakeholder engagement; and viii) monitoring and review.
-
Develop and implement a specific Human Resources Policy.
-
Prepare and implement an independent worker grievance mechanism.
-
Implement the Contingency Plan.
-
Prepare and implement a Security Management Plan.
Key E&S impacts and risks are those typically associated with the construction, and operation and maintenance phases of the power plan, gas pipeline and electric transmission line. These include alteration of land and landscape, removal of vegetation cover, biodiversity alteration, use of hazardous materials, hazardous waste generation, water use, wastewater generation, air quality and pollutant emissions, GHG emissions, noise generation, pesticide use, occupational health and safety risks (work at height, fields magnetic and electrical, substance exposure chemical, occupational accidents and emergencies), contractor management, security risks, land acquisition (gas pipeline and transmission line), cultural heritage and social impacts for nearby communities (El Morro and El Charte). TERMOMECHERO operation does not generate negative social effects on ethnic minorities, involuntary displacement and resettlement. The main positive impacts of E&S include power generation, hiring of local labor, and social support.
Environmental and social key aspects/ 2020:
-
TERMOMECHERO (TMM) and its main contractors (WARTSILA) have developed an Environmental, Social, and Occupational Health and Safety Management System, which it continues to implement in compliance with legal regulations, IFC Performance Standards and World Bank EHS Guidelines.
-
TMM already has the environmental license and the necessary environmental permits for the construction and operation of the project. The power plant, the gas pipeline and the electric transmission line are currently in the operation and maintenance phase. The environmental authority is currently evaluating the request for modification of the environmental license for the expansion of the power plant. TMM has no defaults or liabilities in environmental, social and occupational health and safety matters.
-
In environmental matters, TMM and its contractors have carried out the following activities: i) Training and awareness campaigns. ii) Implementation of the environmental management plan, including waste and wastewater management (final disposal with authorized managers), hazardous materials management, control of polluting emissions, saving and efficient use of water and energy, planting trees and living barriers to control and mitigate noise, pest control, etc. iii) Monitoring of environmental quality through periodic measurements of air quality, atmospheric emissions and noise. iv) Annual quantification of GHG emissions. v) Biotic compensation (to comply with forest compensation obligations, TMM signed an agreement with CORPORINOQUIA for the “Consolidation of protected areas and strategic ecosystems”).
-
Regarding occupational health and safety, TMM and its contractors have carried out the following activities: i) Induction and training. ii) Management of hazardous materials. iii) Delivery of personal protection elements. iv) Analysis of risks and work permits for critical tasks. v) Equipment maintenance. vi) Emergency preparedness and response. vii) Monitoring of employee health conditions (including Covid-19 management). viii) EHS inspections of contractors. ix) Report and monitoring of unsafe conditions, accidents at work and occupational diseases. x) Road safety.
-
In social matters, TMM has been developing activities associated with: i) Information and community participation. ii) Training, education and community awareness. iii) Hiring of local labor. iv) Social compensation (fulfillment of social and labor management commitments, contracting of goods and services with communities, etc.). v) Management of archaeological heritage (during construction). vi) Social responsibility (i.e. energy improvement of the El Morro community).
Sector | Highway infrastructure |
Location | The Concesión Santa Marta – Paraguachón covers the Santa Marta – Riohacha – Paraguachón (Route 90) and Maicao – Carraipia – Paradero (Route 88) routes, Departments of Santa Marta and Guajira, Colombia. |
Investment date | June 2017 |
Overview
The highway corridor that makes up the study area was built in the 90s; currently it is in the operation and maintenance phase. The Concesión Santa Marta Paraguachón S.A., which was established in 1994 under Concession contract No. 445, is responsible for the administration of the project. The object of this concession contract, as provided in article 32, Number 4º of Law 80 of 1993, is to complete studies, definitive designs, rehabilitation and construction works, operation and maintenance of the Río Palomino – Riohacha and Riohacha – Paraguachón stretches, and maintenance of the Santa Marta – Río Palomino sector, Route 90 in the departments of Magdalena and La Guajira.1
The mission of the Concesión Santa Marta Paraguachón S.A. states that it is an organization engaged in administering highway concessions, managing highway infrastructure construction works, providing collection services and complete highway maintenance and operation activities, effectively meeting the needs of their clients through the performance of an excellent team, seeking to generate reasonable dividends for shareholders and benefit to the community overall.
1. On-line review http://troncaldelcaribe.com.co/seccion.php?recordID=1 November 2016
Categorization
The categorization for the (Santa Marta - Paraguachón Toll Road) Sierra Project has been defined as B, based on the following considerations:
-
The concession contractual obligation is operate and maintain the road and tolls, as well as provides the support services such as Restrooms, SOS Emergency Points, Vehicles Maintenance, Vehicles Cranes, among other typical support services.
-
Therefore no construction activities or extension of the right of way is part of the contract. No expansion impacts or greenfield areas are affected;
-
The concession was defined on an existent road built by the government;
-
The activities of operation and maintenance have not generate additional environmental and social impacts or risks in the area or for the shareholders;
-
The project is in compliance with all applicable environmental regulatory permits specifically PAGAS (Management Environmental Measures); Environmental License and Prior Consultation; and
-
The impacts of the project are considered as concentrated, limited and manageable.
The project is located in a specific segment within a National Natural Park, Indigenous Territories and near to other protected environmental areas; however, the applicable permits and requirements have been fulfilled.
Environmental and social aspects
Environmental and social due diligence (“ESDD”), December 2016:
From an environmental and social point of view, according to IFC’s Sustainability Framework, the project represents low risks considering that the scope of the project is limited to highway operation and maintenance activities where impacts that could be caused were evaluated and addressed in PAGAs that are currently being implemented. In addition, it is evident that the company is inclined to maintain successful, satisfactory relationships with the communities and Environmental Authorities (Corpoguajira, Corpamag, ANLA and National Natural Parks), which is considered an opportunity for consolidating the relationships in the long term. Likewise, the Concession has strengthened relations with the non-ethnic communities settled along the highway corridor, municipal and departmental authorities, representatives of the Kogui-Malayo-Arhuaco Indigenous Reserve, and leaders of the Wayuu communities neighboring the Project.
The opportunities of the project including:
-
Update of the management measures collected in the PAGAs that provide recent, real information on the activities currently carried out, which is among the short-term plans of the concessionaire.
-
The project corresponds to a highway corridor that is currently under highway operation and maintenance of a corridor built in the 90s, so it does not involve additional intervention in ecosystems with high environmental sensitivity that were already affected by the national government.
-
Jobs generated for the local communities during the maintenance and operation phase, particularly in activities like clearing, cleaning ROW, security support at collection stations and personnel staffing the toll booth cubicles.
-
The project has current permits and authorizations in force that are necessary for current operation, including: Environmental License for works in the “Los Muchachitos Sector” from ANLA and CORPAMAG, discharge permits, water concession permits, forestry use permits, and the like.
-
The concession has the management and operational capacity to integrate social and environmental aspects under an ESMS.
The formulation and implementation of the environmental and social management system (ESMS) has been required in order to fully comply with IFC standards. This secures a high level of environmental and social performance during the operation of the system. As priority items, the project should run:
-
Update the Environmental Management Measures included in the PAGA for each project sector according to the activities and operations currently being carried out.
-
Prepare and submit specific environmental management measures for operation and maintenance of the Maicao-Carraipia – Paradero (Route 88-01) Sector, formally requesting its inclusion in the La Guajira Highway Operation PAGA by the Environmental Authority.
-
Complement the current existent and applicable information of the project, strengthen and implementing an integrated, centralized and comprehensive environmental and Social Management System (ESMS). The ESMS should incorporate at least the following elements:
i) Policy;
ii) Risk and impact identification (including cumulative and residual risk analysis);
iii) Management programs;
iv) Organizational capacity and competency;
v) Emergency preparation and response;
vi) Implementation of occupational health and safety performance measurement standards;
vii) Stakeholder relations; and
viii) Monitoring and review.
Key E&S impacts and risks are associated with the operation and maintenance phase of a road infrastructure project. These include use of hazardous materials, hazardous waste generation, water use, wastewater generation, rainwater pollution, air quality and pollutant emissions, GHG emissions, noise generation, health and safety risks (occupational accidents, traffic accidents, and emergencies), security risks, contractor management, and social impacts for nearby communities (including social negative effects, such as the affectation of vulnerable groups, involuntary displacement and resettlement). The main positive impacts of E&S include the provision of a high-performance road, the reduction of user travel times, the improvement of traffic, the hiring of local labor and social support.
Environmental and social key aspects/ 2020:
-
Concession Santa Marta - Paraguachón (CSMP) and its main contractors (CONDOR) have developed and implemented an Environmental, Social and Occupational Health and Safety Management System based on national legislation, IFC Performance Standards and World Bank EHS Guidelines.
-
CSMP already has the environmental license and the necessary environmental permits for the operation and maintenance of all project: Santa Marta - Palomino (Route 9008), Palomino - Riohacha (Route 9009), Riohacha - Paraguachón (Route 9010) and Paradero - Maicao (Route 8801), including toll and weigh stations and operational control center. CSMP has been complying with the implementation of the environmental management programs established in the PAGA and PMA. There are no pending environmental obligations related to permits and licenses for the “Sea Wall” and “Muro en Tierra Armada” projects (“La Lengüeta” and “Los Muchachitos” sectors). On 2020-II, CSMP began road maintenance activities (intervention of the asphalt layer) in the Don Diego - Río Palomino sector (“La Lengüeta” sector, Route 9008, within the area of the National Natural Park), in accordance with the environmental authorization granted by PNN.
-
In environmental matters, CSMP and its contractors have carried out the following activities: i) Training and awareness campaigns. ii) Implementation of the environmental management plan, including: waste and wastewater management (construction of domestic wastewater treatment systems, reuse of waste in maintenance activities (asphalt, concrete and plant material), final disposal of solid waste with authorized managers, etc.), management of hazardous materials, control of polluting emissions, saving and efficient use of water and energy, pest control, pruning of vegetation and landscaping. iii) Monitoring of environmental quality through periodic measurements of water, air and noise. iv) Annual quantification of GHG emissions. v) Biotic compensation by planting of fruit trees and ornamental plants.
-
Regarding occupational health and safety, CSMP and its contractors have carried out the following activities: i) Induction and training. ii) Management of hazardous materials. iii) Delivery and use of personal protection elements. iv) Analysis of risks and work permits for critical tasks. v) Equipment and tool maintenance. vi) Emergency preparedness and response. vii) Road safety. viii) Monitoring of employee health conditions (including Covid-19 management). ix) Report and monitoring of unsafe conditions, accidents at work and occupational diseases. x) EHS inspections of contractors.
-
In social matters, CSMP has been developing activities associated with: i) Attention to the user: CSMP has an implemented and disclosed mechanism for the reception, management and timely response of petitions, complaints and claims (grievance mechanism). ii) Information and community participation (“Communicate” and "Neighbors” programs). iii) Hiring of local labor ("Initiatives" program). iv) Training and education (“Road safety” program and “Training” program). v) Recovery of the right of way: Registration and monitoring of environmental complaints to manage with the territorial entities and environmental authorities the events of invasion of the right of way (illegal occupation, inappropriate waste disposal, etc.). vi) Identification and recognition of properties (acts of neighborhood). For the maintenance activities to be carried out on Routes 9008 and 9009, and considering the large number of dwellings located in the road exclusion zone (right of way), Ashmore has recommended to CSMP documenting the social strategy to be implemented for the management of social impacts. vii) Social responsibility: Donations and social support to neighboring communities.
Sector | Electricity |
Location | The Pucallpa Plant CT is located in the district of Yarinacocha, province of Coronel Portillo, Ucayali region, Perú. The Puerto Maldonado Plant CT is located in the district of Tambopata, province of Tambopata, region of Madre de Dios, Perú. |
Investment date | May 2018 |
Overview
Infraestructuras y Energías del Peru S.A.C.’s (IEPSAC) objective is to perform all types of business and activities related directly or indirectly to electricity generation and sale.
IEPSAC operates two thermoelectric centers, the Pucallpa Cold Reserve Plant with a 40-MW generation capacity and the Puerto Maldonado Cold Reserve Plant with a 20-MW generation capacity; the purpose of both plants is to address the supply commitment contracted with the State under the Concession contracts: “Reserva Fría de Generación – Planta de Pucallpa” and “Reserva Fría de Generación – Planta de Puerto Maldonado” (“Cold Reserve Generation – Pucallpa Plant” and “Cold Reserve Generation – Puerto Maldonado Plant”).
That the maximum generation capacity exceeds the capacity required under the contract with COES (Comité de Operación Económica del Sistema Interconectado Nacional [Economic Operation Committee of the National Interconnected System] by 20 MW, as follows:
-
The Pucallpa Plant has a 60-MW generation capacity; however the plant operates at a 40-MW capacity according to the contract signed with COES.
-
The Puerto Maldonado Plant has approved for a 40-MW generation capacity; however the plant operates at a 20-MW capacity according to the contract signed with COES.
Categorization
Category B project according to the IFC’s “Environmental and social review procedures manual” and Environmental and Social (E&S) Management Procedures Ashmore Andean Fund II (AAFII).
Environmental and social aspects
Environmental and social due diligence (“ESDD”), July 2017:
From an environmental and social point of view, considering IFC’s Sustainability Framework, the project represents medium risk. The project´s commitment to prevent, mitigate and solve all possible environmental and social aspects, and to fully comply with national regulations and with the IFC standards.
Both plants are located in an area affected by different industrial and/or special use activities so that the environment is modified and the communities are not considered vulnerable.
Moreover, the negative environmental and social risks and impacts are localized specifically in both plants; they are mainly reversible and easily addressed by means of prevention measures and operational control.
The Pucallpa Plant is in Basic Heavy Industrial zoning with a natural gas fractioning plant and service station as neighbors. While the Puerto Maldonado Plant is within an area zoned for recreational use, the Site is surrounded by properties used as industrial facilities, such as three service stations, a construction materials warehouse and a cement plant.
IEPSAC must be work in to fully comply with IFC Performance Standards and national and local legislation. This secures a high level of environmental and social performance during the operation of the system. As priority items, the project should run:
-
Monitor and comply with the IFC performance standards (PS1 – PS8 as applicable) and the general guidelines (environmental, health and safety general guidelines) and specific sector guidelines of the World Bank (environmental, health and safety guidelines for thermoelectric plants).
-
Comply with the Environmental and Social Action Plan (ESAP)
-
Based on the results of the basic GHG estimates that exceed 25,000 t CO2Eq/ year and according to the PS 3 guidelines, IEPSAC should calculate their GHG emissions annually under actual operational scenarios and define reduction alternatives with these results.
-
Develop a legal requirements matrix and one for environmental and social commitments based on the OEFA / OSINERGMIG regulatory requirements [Environmental Assessment and Regulation Authority (OEFA, per the Spanish acronym) / Energy and Mining Investment Supervisory Authority (OSINERGMIN, per the Spanish acronym)].
-
Implement an external and internal grievance and complaint response mechanism.
-
Implement the Community Relations Plans, prepare specific (written) human resources policies and disseminate them to all workers, and to involve all stakeholders in the Contingency Plan, especially nearby neighbors, must be assumed by senior company management in order to specify it in the short term.
Key E&S impacts and risks are those typically associated with the operation and maintenance phase of a thermoelectric plant. These include hazardous waste generation, water use, wastewater generation and discharge, air quality and atmospheric emissions, GHG emissions, noise generation, risks associated with occupational health and safety, and contractor management. IEPSAC plants are located 2 km from the nearest communities and does not generate negative social effects on ethnic minorities or on cultural heritage. The main positive impacts of E&S include power generation, hiring local labor, and social support.
Environmental and social key aspects/ 2020:
-
EIEPSAC continues to implement the Environmental, Social, and Occupational Health and Safety Management System based on national legislation, IFC Performance Standards, and World Bank EHS Guidelines. However, IEPSAC must make efforts to continue implementing in the short and medium term the actions defined in the ESAP, in order to strengthen its management system.
-
The environmental licenses and permits of IEPSAC are under strict monitoring to ensure their compliance status. IEPSAC has no defaults or liabilities in environmental, social and occupational health and safety matters. IEPSAC is updating the environmental impact studies (ESIA) of both plants. In accordance with Peruvian regulations, these studies must be updated every 5 years and delivered to the competent environmental authority.
-
The solid waste and wastewater generated are delivered to specialized managers who are in charge of its final disposal.
-
Both plants are in cold reserve and come into operation as required by the Peruvian government. To date there are records of less than 1000 hours of operation / year, so no significant atmospheric emissions have been generated. According to regulatory requirements, it is necessary to monitor air quality and fixed sources when 8000 hours of operation / year are exceeded. However, IEPSAC has been carrying out internal measurements in order to verify the operation of the equipment and the expected emissions.
-
Noise reduction and control programs include the use of barriers, acoustic insulation, silencers, and appropriate protective equipment for employees and visitors.
-
IEPSAC facilities comply with what is established in the codes and technical regulations regarding earthquake-resistance, security and emergency systems (F&G, SDE, and FPS), etc. IEPSAC has a contingency plan in each plant with established measures for the prevention, preparation and response to emergencies. All plant personnel are trained in emergency response. The firefighting system is internally tested on a weekly basis and certified annually by a specialized entity. The SSOMA (EHS) team of IEPSAC conducts periodic inspections of emergency response equipment and elements.
-
IEPSAC has been implementing a Community Relations Plan (included in the ESIA), whose main programs are Communication, Labor practices, Social promotion and capacity building, Health care and monitoring, and Citizen Surveillance. Although there are no communities within the plants direct area of influence, IEPSAC has been working with the Villa Primavera and La Joya communities, which are approximately 2 km away, providing information and implementing social programs.
-
IEPSAC has an implemented and disclosed mechanism for the reception, management and timely response of requests, complaints and claims, whose scope extends to stakeholders.
Sector | Construction– mining contractor |
Location | Principal base in Lima, Peru, developing projects in Latin America (Colombia, Panama, Mexico) |
Investment date | April 2018 |
Overview
STRACON S.A.C. began their activities as a company specializing in mining services in 1998 with the El Brocal project. STRACON GyM S.A. is a mining contractor company that provides comprehensive open pit and underground mining construction operations covering all phases of a mining project from planning, development, construction, and operation up to mine closure.
STRACON GyM S.A. provides the following mining construction and operation services:
- Construction
- Mine infrastructure construction (tailings dams, dikes, wells, reservoirs, etc.)
- Area preparation and cleanup (earth moving services)
- Access and haul road construction
- Construction of workshops, camps, fuel stations, and magazines
- Engineering development and project management
- Operation
- Drilling and blasting
- Loading and haulage
- Fleet operation and maintenance
- Construction, operation, and closure of mine
STRACON GyM S.A.´s main office is located on Surquillo, Lima, and Perú. Administrative offices are installed at mining units where projects are carried out in Peru and abroad. Projects completed abroad are managed through local representatives with legal status in the country of the project.
In 2015 and 2016, STRACON GyM S.A. was recognized by the Good Employer Association (Asociación de Buenos Empleadores – ABE) as one of the best companies to work for. They were also recognized by MAPFRE during the same period as the best mining contractor for Safety Excellence.
STRACON GyM S.A. has a robust Corporate Integrated Management System (Environment, Occupational Health and Safety and Quality) aligned with OHSAS 18001:2007 and ISO 14001:2015 standards, which is designed under the concept of continuous improvement. The SIG has 20 elements to enable it to manage the risks and impacts of their activities:
- SIG – 01 Senior management commitment and leadership
- SIG – 02 Risk Management and Control
- SIG – 03 Legal and other type requirements
- SIG – 04 Planning and decision-making
- SIG – 05 Positions, responsibilities and resources
- SIG – 06 Training, competence and awareness
- SIG – 07 Communication and report preparation
- SIG – 08 Document control and records management
- SIG – 09 Management of Change
- SIG – 10 Corporate governance
- SIG – 11 Supply chain management
- SIG – 12 Subcontractor management
- SIG – 13 Product preparation
- SIG – 14 Operational control
- SIG – 15 Emergency preparation and response
- SIG – 16 Monitoring and measurement
- SIG – 17 Preventive and corrective actions
- SIG – 18 Inspection and observation of behavior
- SIG – 19 Internal audit
- SIG – 20 Senior management review
In addition, the following social management documents are included in the SGyM SIG:
- Social responsibility policy;
- Grievance Procedure;
- Stakeholder communication;
- Crisis management plan;
- Crisis plan for strikes and stoppages in Perú
Categorization
Category B+ project according to the IFC’s “Environmental and social review procedures manual” and Environmental and Social (E&S) Management Procedures Ashmore Andean Fund II (AAFII).
Environmental and social aspects
Environmental and social due diligence (“ESDD”), January 2018:
From an environmental and social point of view, considering IFC’s Sustainability Framework, the project represents medium risk. The project´s commitment to prevent, mitigate and solve all possible environmental and social aspects, and to fully comply with national regulations and with the IFC standards.
No material risks related to Occupational and Safety and the Environment were identified due to proper application of SGyM’s SIG. Considering the sample project selected (La Arena), it was evident that the SIG requirements are properly applied. No material findings were identified in countries where SGyM has operations from the reputational point of view and as a result of monitoring the media.
Risks associated with SGyM activities are properly managed through the SIG. SGyM has good performance in SSOMA recognized by mining customers, which is a strength that can be used in mining project tender processes. SGyM’s SIG is robust and has a focus on continuous improvement that can identify risks early. Moreover, accidents and incidents occurring were opportunities to improve work processes and procedures to ensure that they are not repeated.
SGyM’s SIG is aligned with AAFII A&S requirements and the most of requirements of IFC Performance Standards. The SIG must be completed in to fully comply with IFC Performance Standards. This secures a high level of environmental and social performance during the operation of the system. As priority items, the project should run:
- Incorporate the Social Responsibility Area in the organizational structure of SIG management, or define communication channels and links among them.
- Incorporate management programs of the Social Responsibility Area into the SIG Management organizational structure or define communication channels and links among them.
- SGyM’s SIG implementation and compliance in the different projects it carries out must be verified as part of the monitoring and control process (set out in this ESAP and report).
- Develop a HR policy aligned with the requirements of the IFC's PS.
- Re-orient workers on the grievance response system (at least annually, if not more often, depending on the characteristics of each project); also reinforce the use of this tool with workers, which must keep records available on actions implemented.
- Based on the results of the basic GHG estimates that exceed 25,000 t CO2Eq/ year and according to the PS 3 guidelines, STRACON GyM should calculate their GHG emissions annually under actual operational scenarios and define reduction alternatives with these results.
- Follow and comply with IFC performance standards (PS1 – PS8 as applicable) and the general IFC and World Bank guidelines on the environment, health and safety, and specific sector guidelines of the World Bank and environmental, health and safety guidelines for the mining sector (sections applicable to SGyM operations).
- Comply with the Environmental and Social Action Plan (ESAP).
Key environmental and social impacts and risks are associated with mining project construction and operation activities. These include alteration of land and landscape, erosion and sedimentation, use of hazardous materials, hazardous waste generation, water use, wastewater generation, rainwater pollution, air quality and pollutant emissions, GHG emissions, noise generation, health and safety risks (occupational accidents, traffic accidents, and emergencies), security risks, and social impacts such as generation of expectations and affectation of significant cultural heritage sites. STRACON´s activities does not generate social negative effects such as affectation of vulnerable groups or ethnic minorities. The main positive impacts of E&S include hiring of local labor and social support.
Environmental and social key aspects/ 2020:
-
STRACON has developed an Environmental, Social, and Occupational Health and Safety Management System (SIG), which it continues to implement in compliance with legal regulations, IFC Performance Standards, World Bank EHS Guidelines, and ISO9001 (Quality), ISO14001 (Environmental and Social), ISO45001 (Occupational Health and Safety) standards.
-
STRACON does not require licenses, permits or environmental authorizations. In the different projects, STRACON’s clients are responsible for obtaining and complying with the required environmental permits. All contracts signed by STRACON and its clients establish requirements to comply with environmental and health and safety regulations.
-
Although the natural resources used and the pollution control systems are framed in the licenses and environmental permits of the mines (and under the responsibility of each client), STRACON has corporate indicators of environmental performance and the following environmental management plans/programs/standards that it implements in the development of its operations: Saving and efficient use of resources (water, energy, fuels, paper); Comprehensive waste management; Management of sedimentation ponds; Soil management and treatment contaminated; GHG management; Preservation of flora and fauna; Management before archaeological discovery, etc. STRACON has been carrying out annual GHG measurements based on an implemented standard for GHG and energy management. Due to the nature of the company, almost the total GHG emissions generated are due to fuel consumption (use of machinery, equipment and vehicles). Therefore, the reduction actions implemented are limitation of the age of vehicles, preventive maintenance, and training of operators for the optimal use of machinery and equipment.
-
The occupational health and safety management system is framed within the SIG and aligned with the ISO45001 standard. Its main procedures, plans and programs for the control of risks in OHS are: Control of critical tasks (work at height, confined spaces, movement of heavy machinery, electrical work, welding, handling of explosives, lifting of cargo); Safe work analysis; Work permit system; Occupational health and hygiene; Covid-19 prevention and management; SSOMA (EHS) training; Reporting and investigation of accidents; Handling of hydrocarbons and flammable liquids; Preventive and corrective maintenance of machinery and equipment; Internal traffic regulations; Delivery and use of personal protections elements; etc. STRACON has an implemented and disclosed standard for emergency preparedness and response that includes the identification, planning and effective response to emergencies. STRACON also has a crisis management plan in place that covers environmental emergencies, damage to property and physical security. The implementation of a preventive and corrective maintenance plan for machinery, equipment and vehicles is also highlighted in order to ensure their condition and operation.
-
Most STRACON projects are located outside urban centers, so there is no direct impact on communities. The social management in the projects where STRACON operates is in charge of the clients, so the interaction with the community is limited. However, STRACON carries out the following activities within the framework of its CSR Policy: i) Hiring of unskilled labor in the areas of influence of the projects; ii) Support to providers of goods and services in the communities; iii) Training and education in practical trades to nearby communities; iv) Donations.
-
Although communication and participation activities with external stakeholders in mining projects are the direct responsibility of each client, STRACON has an implemented and disclosed procedure for complaints and claims whose scope extends to stakeholders, and a communication procedure with interested parties. STRACON has an ethical, independent and anonymous line, which facilitates the reception and management of external and internal requests, complaints and claims.
Sector | Transportation |
Location | The project is located within the perimeter of Bogotá, Colombia. The area of influence is specifically defined by the areas of temporary storage (and only for the duration of this task) for the parking of the vehicle fleet before delivery to TRANSMILENIO and the administrative areas (office) established by the concessionaire. |
Investment date | December 2018 |
Overview
Concessionaire for the provision of the public passenger public transport service in its fleet provision component of the TRANSMILENIO System (Massive Public Transportation System of Bogotá). TRANSINNOVA has been awarded the bid for the replacement of the buses of the Usme Portal of TRANSMILENIO, being this bidding process the most important offered by the District of Bogota in 2018. The award includes the entry of 158 biarticulated and 92 articulated Volvo vehicles with Euro V Diesel technology that reduces gas emissions. These vehicles will enter the system in two phases: Phase 1 will be in October 2019, and Phase 2 in July 2020. Among the general obligations of TRANSINNOVA, as a fleet provision concessionaire, are:
Pre-operative stage:
-
During the manufacturing process, supervise in a coordinated manner with the operation concessionaire so that the specifications required of the bus fleet are met. This monitoring does not contemplate the assurance of the management of environmental and OHS aspects. For this, certifications must be requested that reflect the management implemented by the company in charge of the construction of the vehicle fleet.
-
Fleet parking from its entry into Colombia (either chassis or complete buses) until delivery to TRANSMILENIO. As part of this scope, activities such as vehicle washing or maintenance are not contemplated. Only activities are considered of physical security.
-
Make the import and nationalization procedures for the bus fleet.
-
Provide a maintenance manual to TRANSMILENIO, which will be the guide of the operation concessionaire to carry out the maintenance of the fleet.
Operation and maintenance stage:
-
Verify the status of assets (specific operation and maintenance activities shall be the responsibility of another concessionaire).
-
Review and monitor the maintenance activities carried out by the fleet operation concessionaire.
-
Send TRANSMILENIO monthly maintenance monitoring reports.
Disengagement stage:
-
Conclude the process of untying the fleet.
-
Receipt, parking and scrapping process of fleet.
Categorization
Category B project according to the IFC’s “Environmental and social review procedures manual” and Environmental and Social (E&S) Management Procedures Ashmore Andean Fund II (AAFII).
The impacts that could result from the activities of this type of project are characterized by having a punctual extension and of low magnitude, since the activities contemplated are focused on the purchase of the vehicle fleet for the TRANSMILENIO transport system, storage and parking. Temporary leased land (already developed), and subsequent delivery to the system for operation and maintenance by another concessionaire. Additionally, in the face of potential impacts, it is identified that they are preventable and mitigable with the adequate implementation of the management measures and the actions that TRANSINNOVA must implement included in the Environmental and Social Action Plan (ESAP). On the other hand, for the development of the project, the construction or development of new areas or facilities. For example, the construction of the vehicle fleet will be carried out in workshops, headquarters of suppliers, so it is not requires the construction of works, and infrastructure for manufacturing, as well as temporary parking areas and offices will be leased.
Environmental and social aspects
Environmental and social due diligence (“ESDD”), 2018:
From the environmental and social point of view, considering IFC’s Sustainability Framework, the project represents low risk. According to the characteristics of the project and the scope of the fleet provision concessionaire, the need to apply for environmental permits is not considered. Regarding the use of resources, these will be mainly associated with the consumption of energy and water resources in the administrative offices and to a lesser extent in the temporary parking lot of the fleet. In relation to these activities, the generation of conventional and hazardous waste (associated with waste electrical and electronic equipment - WEEE) is only foreseen in the administrative areas, which must be managed with the public cleaning services company in the case of conventional waste and with companies with an environmental license in the case of hazardous waste. Finally, during the decommissioning phase, which considers junking of the vehicle fleet, the concessionaire shall ensure that this activity is carried out by third parties with the corresponding, applicable environmental permits and licenses.
The formulation and implementation of the Environmental and Social Management System (ESMS) has been required in order to comply with IFC Performance Standards. This secures a high level of environmental and social performance during the operation of the system. As priority items, the project should run:
-
Follow and comply with IFC PS (PS1 – PS4, as applicable) and World Bank General EHS Guidelines.
-
Comply with the Environmental and Social Action Plan (ESAP).
-
Carry out a comparative analysis of the emissions generated by the current fleet versus the emissions generated by the current fleet versus the emissions generated by the new fleet, with the aim of having a documentary support that reflects the environmental benefits generated by the project (GHG annual quantification).
-
Disclosure to interest groups.
Key E&S impacts and risks are those typically associated with administrative and monitoring activities derived of the fleet supply process. These include waste and wastewater generation, health and safety risks (occupational accidents and emergencies), supplier management and security risks. TRANSINNOVA’s operation does not generate social negative effects. The main positive impacts of E&S include the provision of a new bus fleet for Bogotá's mass transportation system.
Environmental and social key aspects/ 2020:
-
TRANSINNOVA has already completed the design phase of the Environmental, Social, and Occupational Health and Safety Management System (100% progress), and is currently developing the implementation and verification phases with the support of the consulting company Ápice Ingeniería S.A.S. In the implementation phase, training, evaluation and dissemination activities of the management system are underway. In the framework of the verification phase, work has been done on the plan and schedule of audits, and on the recording of information to feed the indicators of the management system. In the framework of this process, compliance with the legal requirements, IFC Performance Standards, and the other requirements established in the Environmental and Social Action Plan (ESAP) for the pre-operational stage (importation of fleet) and for the operational stage (fleet inspection already operational in the facilities of the operational concessionaire) has been ensured.
-
The permits and authorizations of the TRANSINNOVA are in force and in compliance. TRANSINNOVA has no defaults or liabilities in environmental, social and occupational health and safety matters.
-
TRANSINNOVA has implemented and disclosed mechanism for the reception, management and timely response of petitions, complaints and claims (grievance mechanism).
Sector | Transportation |
Location | The project is located within the perimeter of Bogotá, Colombia. The area of influence is specifically defined by the areas of temporary storage (and only for the duration of this task) for the parking of the vehicle fleet before delivery to SITP and the administrative areas (office) established by the concessionaire. |
Investment date | November 2019 |
Overview
Concessionaire responsible for purchase of the electric fleet for the zone component of the Integrated Public Transportation System (Sistema Integrado de Transporte Público –SITP) public passenger transportation service. As a result of the Abbreviated Selection of Minor Amount process advanced in the second semester of 2019 by TRANSMILENIO, Concession contract No. 769 was signed of 2019 with the company ELECTRIBUS BOGOTA FONTIBON II S.A.S, for the provision of the electric fleet of the zonal component of the public passenger transport service of the integrated public transport system (SITP).
The object of the contract is the supply of 126 standard-type buses with capacity for 80 passengers, 100% electric, for the Fontibón II area. Likewise, the Concession contract No. 770 of 2019 was signed with the company ELECTRIBUS BOGOTA USME I S.A.S, for the provision of the electric fleet of the zonal component of the public passenger transport service of the integrated public transport system SITP.
The object of the contract is the supply of 120 standard-type buses with capacity for 80 passengers and 13 buseton-type buses with a capacity of 50 passengers, 100% electric, for the Usme I area. With this type of contracts, the entity intends to introduce electric transport technology into the integrated public transport system SITP of the city of Bogotá.
For the fulfillment of its contractual obligations, ELECTRIBUS companies have selected the CONSORCIO ELECTRIC BOGOTA, made up of BYD AUTO INDUSTRY and BYD MOTOR COLOMBIA S.A.S companies as the manufacturer and supplier of the buses, in accordance with the technical specifications contemplated in the concession contract.
Among the general obligations of ELECTRIBUS, as a fleet provision concessionaire, areAmong the general obligations of ELECTRIBUS, as a fleet provision concessionaire, are:
Pre-operative stage:
-
Supervise manufacture, assembly, body staging, and the like, and require the Manufacturer to correct any defect in the fleet prior to delivery and ensure that such repairs are effectuated without affecting the fleet delivery plan. During the manufacturing process, the provision concessionaire shall supervise as necessary and in coordination with the operation concessionaire such that the required vehicle specifications are met. This monitoring does not contemplate the assurance of the management of environmental and OHS aspects. For this, certifications must be requested that reflect the management implemented by the company in charge of the construction of the fleet.
-
Fleet parking from its entry into Colombia (either chassis or complete buses) until delivery to TRANSMILENIO and thus the operation concessionaire, except where this risk is assumed by the Manufacturer in which case the obligation of the provision concessionaire begins from the moment of Manufacturer delivery until delivery to TRANSMILENIO.
-
Make the import and nationalization procedures for the electric fleet.
-
Provide a maintenance manual to TRANSMILENIO, which will be the guide of the operation concessionaire to carry out the maintenance of the electric fleet.
-
Ensure that all technical specifications necessary are reported so that the charging system of the power substations at the yards can completely charge the batteries (100%) in a period no greater than four (4) hours and that the vehicle charging connections are compatible with the recharge system infrastructure.
Operation and maintenance stage:
-
Verify the status of assets (specific operation and maintenance activities shall be the responsibility of another concessionaire).
-
Review and monitor the maintenance activities carried out by the fleet operation concessionaire.
-
Send TRANSMILENIO monthly maintenance monitoring reports.
Disengagement stage:
-
Conclude the process of untying the fleet.
-
Receipt, parking and scrapping process of fleet.
Categorization
Category B project according to the IFC’s “Environmental and social review procedures manual” and Environmental and Social (E&S) Management Procedures Ashmore Andean Fund II (AAFII).
The impacts that could arise from the activities required for this type of project are characterized by specific extent and small size since the activities contemplated focus on the purchase of the electric fleet of the public passenger transportation service zone component of the Sistema Integrado de Transporte Público (SITP), operation, maintenance and temporary parking on leased land (already developed). In addition, it is determined in view of the potential impacts that they can be prevented and mitigated with proper implementation of management measures and actions that the organization must implement that are included in the Environmental and Social Action Plan (ESAP). Moreover, construction or development of new areas or facilities is not expected. Construction of the vehicle fleet will be completed in workshops and home offices of the suppliers, for example, therefore construction of works and facilities will not be required for its manufacture. Likewise, the temporary parking areas and offices will be leased.
Environmental and social aspects
Environmental and social due diligence (“ESDD”), 2019:
From the environmental and social point of view, considering IFC’s Sustainability Framework, the project represents low risk. According to the characteristics of the project and the scope of the electric fleet provision concessionaire, the need to apply for environmental permits is not considered. Resource use shall be primarily associated with power use of the vehicle fleet and administrative offices and water resource in administrative offices and, to a lesser degree, in the fleet temporary parking yard. Only conventional and hazardous waste (associated with electrical and electronic device [WEEE] and batteries at the end of their useful life) in administrative areas is anticipated. Conventional waste shall be managed by a public waste service company and hazardous waste by companies with environmental license. Finally, during the decommissioning phase, which considers junking of the vehicle fleet, the concessionaire shall ensure that this activity is carried out by third parties with the corresponding, applicable environmental permits and licenses. The formulation and implementation of the Environmental and Social Management System (ESMS) has been required in order to comply with IFC Performance Standards. This secures a high level of environmental and social performance during the operation of the system. As priority items, the project should run:
-
Follow and comply with IFC PS (PS1 – PS4, as applicable) and World Bank General EHS Guidelines.
-
Comply with the Environmental and Social Action Plan (ESAP).
-
Perform a comparative analysis of the emissions generated by the current fleet in comparison with the zero to low emissions generated by the new electric fleet in order to have documentary support that reflects the environmental benefits generated by the project.
-
Disclosure to interest groups.
Key E&S impacts and risks are those typically associated with administrative and monitoring activities derived of the electric fleet supply process. These include waste and wastewater generation, health and safety risks (occupational accidents and emergencies), supplier management and security risks. ELECTRIBUS’s operation does not generate social negative effects. The main positive impacts of E&S include the provision of fleet with clean technology for Bogotá's mass transportation system.
Environmental and social key aspects/ 2020:
-
ELECTRIBUS (Usme and Fontibón) has already completed the design phase of the Environmental, Social and Occupational Health and Safety Management System (100% complete), and is currently developing the implementation and verification phases, with the support of the consulting company Ápice Ingeniería S.A.S. In the framework of this process, compliance with the legal requirements, the IFC Performance Standards, and the other requirements established in the Environmental and Social Action Plan (ESAP) has been ensured.
-
To date, and through BYD Colombia as a fleet provider, and with the assurance of ELECTRIBUS, the following activities continue to be carried out: Supervision of fleet manufacturing, importation, nationalization, approval and authorization to provide the public passenger transport service. The first package of electric buses arrived in Colombia, imported from China, at the end of August 2020 (40 buses). The connection to the SITP and the delivery to the operation concessionaire will be made in 2021 in two deliveries, one per functional unit (Usme and Fontibón).
-
The permits and authorizations of the ELECTRIBUS are in force and in compliance. ELECTRIBUS has no defaults or liabilities in environmental, social and occupational health and safety matters.
-
ELECTRIBUS has implemented and disclosed mechanism for the reception, management and timely response of petitions, complaints and claims (grievance mechanism).
Sector | Transportation / Roads |
Location | Barranquilla, Colombia |
Investment date | May 2020 |
Overview
Definitive studies and designs, financing, social, property and environmental management, construction, rehabilitation, administration, operation and maintenance of the loading and port access of the Barranquilla District and the basic canal system of La Ahuyama between the Alberto Pumarejo bridge and Cra. 38 (Av. de Los Estudiantes). Two toll plazas are located along the route (4.3 Km), the first called “Barranquillita” at Carrera 46 with Calle 6, and the second “Zona Franca” [Free Zone] divided into two stations, North and South (one constructed far from the other because of availability of road width), located at the beginning and end of the corridor. The start date of concession contract No. VF-12-2010-02 is December 23, 2010 and considers that the operation phase of 156 months (13 years) will be completed on January 23, 2025. However, this date was extended to the year 2038. The current project phase (O&M), includes the following actions:
Basic services:
-
Routine road maintenance (cleaning drains, pavement, pavement repair, sealing fissures and crevices, replacement of slabs, platforms and curbs).
-
Environmental management and control (maintenance of environmental works of the La Ahuyama canal).
-
Traffic operation and monitoring, including weighing operations.
-
Toll collection.
-
Security of facilities and safekeeping of the right of way.
-
Communication with the Operation Control Center (CCO).
-
Report preparation and delivery.
Complementary services:
-
Towing service (vehicle up to 60 tons and hoist of 30 tons).
-
First aid for accident victims.
-
Emergency mechanical assistance (vehicle workshop).
-
Road inspection (routine, signage, traffic, safety, comfortable ride).
-
Vehicle weighing (periodic operations).
Categorization
Category B project according to the IFC’s “Environmental and social review procedures manual” and Environmental and Social (E&S) Management Procedures Ashmore Andean Fund II (AAFII).
Environmental and social aspects
Environmental and social due diligence (“ESDD”), 2019:
From an environmental and social point of view, considering IFC’s Sustainability Framework, the project represents medium risk. The project´s commitment is to prevent, mitigate and solve all possible environmental and social aspects, and to comply with national regulations and with the IFC Performance Standards.
The project performance in regard to the risks and opportunities of its activities should be strengthened in the sense of articulating management among the different areas as well as temporary hiring of a professional to support the process of implementing the management system and a professional to support the property management process. It is evident that the risks to which workers are exposed in carrying out critical and routine activities have been identified as priority. Nevertheless, environmental and social risks and impacts have not been analyzed, evaluated and mitigated in a timely and appropriate manner. There is non-compliance with some obligations set forth in the environmental license and the water concession permit in regard to environmental matters.
The area where the Barranquilla District Freight and Port Access Corridor is located is near the Magdalena River, the area where the port sector was developed around an industrial zone. The Free Zone, Barranquilla Port Company, customs facilities, transportation companies, heavy freight vehicle parking, warehouses, and logistics and freight companies are in this vicinity. There are also residential areas around the industrial zone as well as sectors invaded that were occupied by families arriving in the city due to displacement and which continue settling in the areas nearest the Rebolo, La Ahuyama and Los Tramposos canals. Resolution 1710 dated October 28, 2011 (environmental license) established the La Luz, La Chinita and Rebollo neighborhoods as the project area of influence. The territorial extent where the activities are carried out are expanded to 50 meters from side to side of the road. During the construction phase of the project, one hundred and twenty-eight families were relocated in the invasion zone called Bendición de Dios, in the Carrera 46 sector of Calle 6, a process that was completed with the support of the Barranquilla District. According to S.F. CONVIAS, the social risks related to the resettlement of the population, recovery and purchase of properties, public consultations, etc., were assumed by the District of Barranquilla with the company Empresa de Desarrollo Urbano de Barranquilla SA -EDUBAR under the contract "Design and completion of the property acquisition and resettlement plan”.
S.F. CONVIAS must be work in to fully comply with IFC Performance Standards and national and local legislation. This secures a high level of environmental and social performance during the operation of the system. As priority items, the project should run:
-
Comply in a timely fashion with the obligations set forth in the environmental license and environmental permits.
-
Strengthen the development and implementation of the Integrated Management System (SGI, in Spanish) in a timely fashion.
-
Identify environmental, social and OHS risks and impacts since the activities it carries out are currently in the operation and maintenance phase. Moreover, measures to control and prevent these risks and impacts must be identified and applied.
-
Follow and comply with IFC performance standards (PS1 – PS8, as applicable) and World Bank EHS Guidelines.
-
Comply with the Environmental and Social Action Plan (ESAP).
-
Temporary hiring of a series of professionals to support the process of implementing the SGI and property management associated with the project.
Key E&S impacts and risks are associated with the operation and maintenance phase of a road infrastructure project. These include use of hazardous materials, hazardous waste generation, water use, wastewater generation, rainwater pollution, air quality and pollutant emissions, GHG emissions, noise generation, health and safety risks (occupational accidents, traffic accidents, and emergencies), security risks, contractor management, and social impacts for nearby communities (including social negative effects, such as the affectation of vulnerable groups, involuntary displacement and resettlement). The main positive impacts of E&S include the provision of a high-performance road, the improvement of traffic, the hiring of local labor and social support.
Environmental and social key aspects/ 2020:
-
S.F. CONVIAS began in 2020 with the design and implementation of the Environmental, Social, and Occupational Health and Safety Management System in compliance with current regulations, the IFC Performance Standards, and the requirements established in the Environmental Action Plan and Social (ESAP).
-
S.F. CONVIAS hired at the end of 2020 a specialized external consultant to manage the findings of the ESDD process and implement the actions established in the ESAP, especially those related to gaps in compliance with environmental regulations.
-
Design activities were developed for the reconstruction and reactivation of the nursery, which will allow to have replacement seedlings for the landscaping of the port corridor.
-
In terms of social management, S.F. CONVIAS have been implementing the following programs: i) Development of the “Comunicar Program”, in which flyers are delivered to the community of Avenida Hamburgo to inform about the development of cleaning activities in the rainwater drainage system and pedestrian platform of the road. The community is requested not to dispose of solid waste or wastewaters in the drains. ii) S.F. CONVIAS solidarity campaign, by collecting non-perishable food to donate to the Bendición de Dios community, and support in the logistics of donation delivery by companies allied to this same community.
-
S.F. CONVIAS is implementing and disseminating the mechanism for the receipt, management and timely response of petitions, complaints and claims (complaints mechanism).